One organisation. Endless possibilities. That is the corporate motto of Advanced Composite Structures Australia (ACS-A), and no exaggeration for this innovative local stalwart which has solved endless conundrums for customers.
A trailblazer in the advanced fibre composite space, ACS-A has designed for vertical take-off and landing devices (VTOL), created solutions for theme park challenges, and developed a novel solution for leaking oil and gas pipelines.
The Cluster team caught up with ACS-A’s Dr Paul Falzon last week.
“Doing things the way we have always done — that is not the way we think as an organisation,” says General Manager Paul Falzon. “It stems from the environment that the company is spun out from, in terms of being a highly developmental environment and being used to working that way.”
“Doing things the way we have always done — that is not the way we think as an organisation,”
– General Manager Dr Paul Falzon.
ACS-A has been in operation since 1991, originally under the federally-funded auspices of the Cooperative Research Centre (CRC) Program. It has become known globally for solving problems in novel ways and has worked with major companies, research organisations, and government entities.
Dr Falzon was an original intake to the CRC for Advanced Composite Structures as a PhD student, after finishing an aerospace engineering degree at RMIT. He later became more involved on the commercial side and was appointed general manager in 2014.
After initially focusing on aerospace, ACS-A has since worked across a broad range of industries, from maritime and marine, to defence, oil and gas, rail, civil infrastructure and consumer goods.
Among the varied work already completed by ACS-A are: carbon composite components for large theme park attractions, designing for the latest Martin Jetpack personal aviation – or VTOL – device, a custom enclosure for a gas spectrum analyser camera system, a novel composite clamp for leaking pipelines for PETRONAS, a portable composite stair system for railway personnel, assisting Omni Tanker to upgrade to closed-moulding resin infusion for the manufacture of components, a flange fitting for joining high-pressure pipelines within the oil and gas industry, and a working replacement solution for the aging panels in the F-111 aircraft.
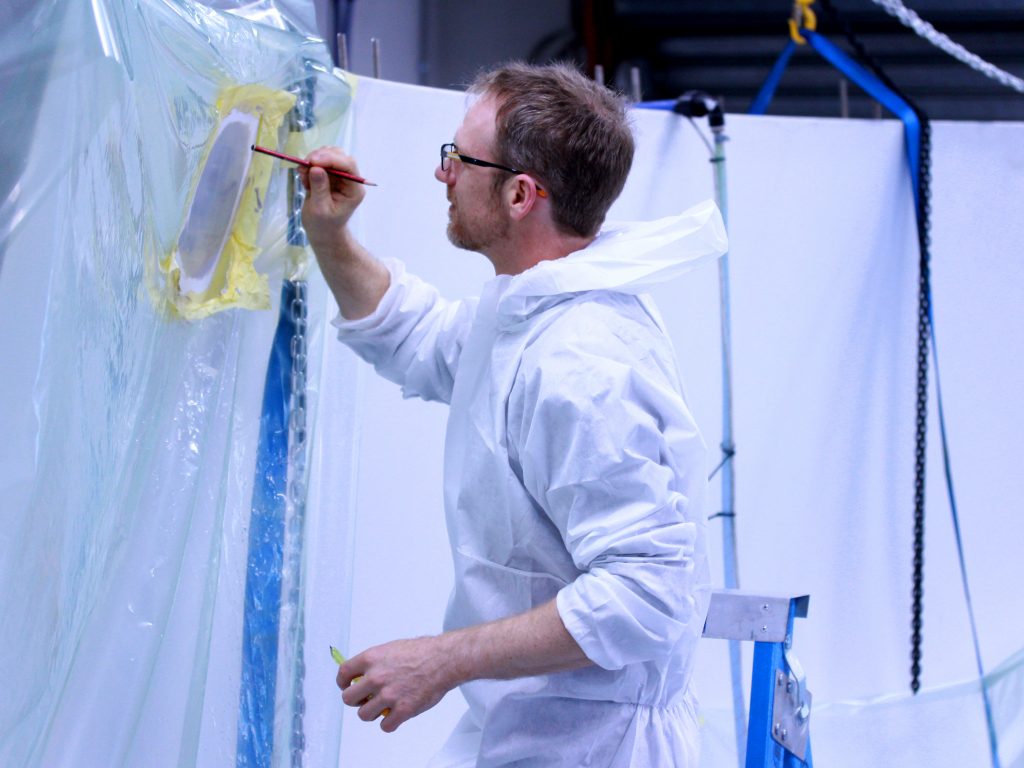
“What we started to find was that the skills and knowledge we had were also applicable to other industries,” Dr Falzon says. “The great thing is that sectors go through their different cycles. When business is slow, R&D is the sort of thing companies tend not to spend money on, so things can get quiet for us, but then we have other industries that are more buoyant. If things are quiet for us in aerospace we can look at rail.”
ACS-A has progressed from its origins in engineering services and four years ago began low-volume, bespoke manufacturing for customers, with in-house capability for niche advanced manufacturing of composite products and assemblies for highly demanding, safety-critical applications. The team gives advice on the best combination of materials and processes for composites applications, including helping to develop new materials.
This “one-stop-shop” solution is a faster route to market, and ACS-A is now looking at larger volume possibilities in the consumer market.
“We have moved into manufacturing and we are doing some internal work at the moment looking at some products that we can have as our own, things that we can bring to market,” Dr Falzon says.
Over 25 years, the firm has gained experience in the use of modelling tools to predict material and component behaviour. This reduces experimentation during the design process, cutting development time and cost.
“The knowledge builds up over the years, particularly working across a broad spectrum of industries. You pick up things, the needs of those industries and how they go about things and the challenges you face to bring new applications into those industries,” says Dr Falzon.
“We might have a company that has been building a composite product for a long time but they want to make it better, design it better, make it more efficient and more cost-effective, or improve or change its performance, so we will run programs for a redesign, go through the process of building a prototype, testing and then give them the solution. Or we might have a company that doesn’t really care what the solution is but they have a problem they want solved.”
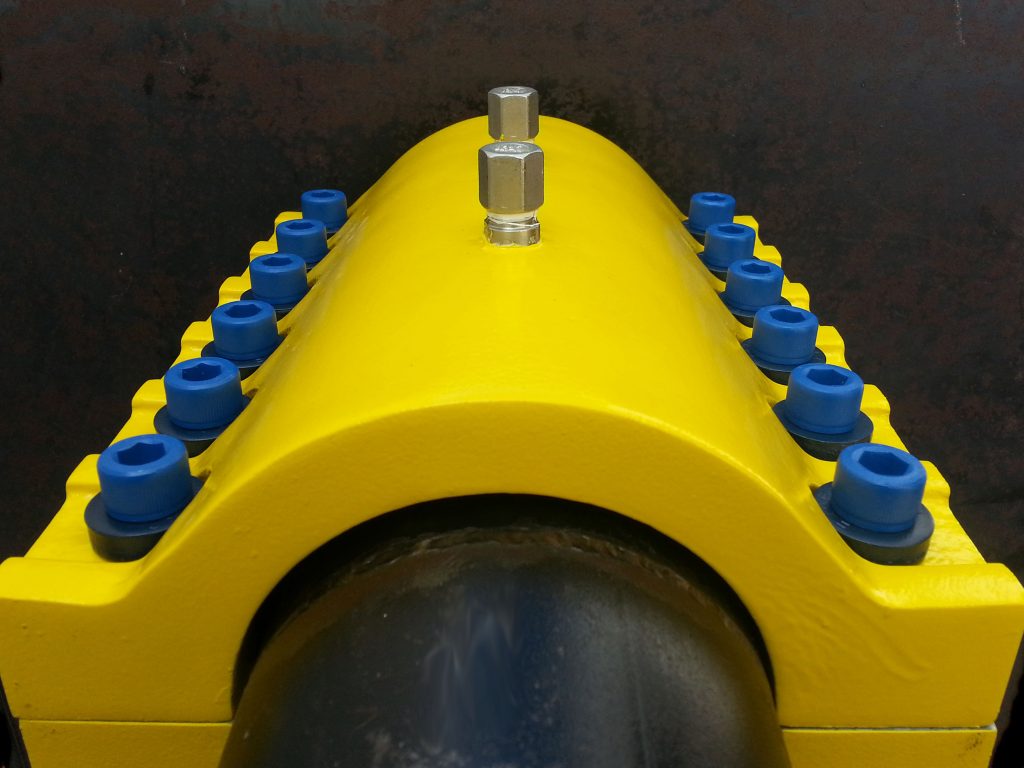
Right now, ACS-A is involved in simulation for an aerospace client in China to assess how the structure behaves under certain loading events such as a birdstrike as part of a certification program.
Past projects have also looked at sustainable fibres, working with hemp, kenaf and flax, and how those fibres could be used to manufacture composite products, for example an extruded product that can be used in the building industry for things like decking. ACS-A found that while the natural fibres are cheap and fast to grow, the cost to extract the fibre and the variable properties which affected structural performance were obstacles.
“It comes down to what the drivers are and what the market demand will be. We spent several years on it but at the end of the day we could not find a pathway to be able to commercialise it as a way forward. Things can change but that was our experience. When we tried to push them into more structural applications we found challenges,” Dr Falzon says.
Now, the ACS-A team is excited by the “blue economy” and is a participant to a new CRC in the aquaculture industry in Australia, and the offshore renewable energy space.
“We are quite keen to get more experience and more involvement in that sector and excited with some of the opportunities there may be for an organisation like ourselves,” Dr Falzon says, explaining that structures enabling fish farms to be moved further offshore is one opportunity.
ACS-A plans to continue to service as many industries as it can into the future.
“We are very flexible, we can work with small customers through to larger customers. You have got to learn to work with companies who are multinationals like an Airbus and then work with a little outfit who are very small and want to develop a new niche product. So you are dealing with very different industries but also very different sizes of organisations within those industries as well,” says Dr Falzon.
“Companies will come to us because of our track record. They know what we have delivered in the past so they are confident that we will be able to deliver what they are after,” he says.
We’ll be featuring more innovative companies in the AFCG Newsletter throughout 2020.
Read our Carbon Revolution Member Profile here.
Feb 2020